SERVICE
Research and Development

Research and Development
Since 2018, Yalong has integrated lean production principles into its operational strategy, significantly improving production efficiency and reducing waste. Additionally, the adoption of an advanced ERP system enables us to streamline operations, optimize resource allocation, and maintain consistent product quality. With a dedicated research and development team, Yalong continuously invests in innovation to enhance product performance and expand our valve range. Our R&D efforts ensure that we stay ahead of market trends and offer solutions that meet the evolving needs of our global customers.
Understanding the diverse needs of our clients, we provide tailored valve solutions that address specific market demands. Our dedicated customer service team ensures that all inquiries are handled promptly, while our after-sales support guarantees client satisfaction with every aspect of their experience.
Production Strength
Marketing Strength

Global Market Coverage and Customer Trust
Yalong Valve
Yalong has established a strong presence in global markets, exporting products to over 50 countries across Europe, North America, Asia, and the Middle East. Our long-term partnerships with key clients worldwide reflect the trust and satisfaction we have earned over the past 25 years.

Multichannel Marketing Strategy
Yalong Valve
We employ a diversified marketing strategy, utilizing both online platforms and offline channels. In addition to maintaining a strong online presence through our official website and social media, Yalong participates in prominent international trade fairs such as the Canton Fair and ISH Frankfurt, connecting with clients and partners face-to-face.

Customer Customization and Service
Yalong Valve
Understanding the diverse needs of our clients, we provide tailored valve solutions that address specific market demands. Our dedicated customer service team ensures that all inquiries are handled promptly, and our after-sales support guarantees that clients are satisfied with every aspect of their experience
FAQ
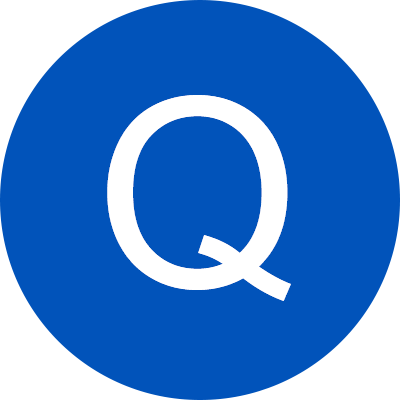
purchase of valves, in addition to price, what factors should be considered?
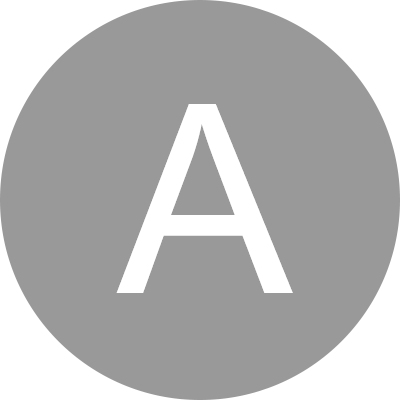
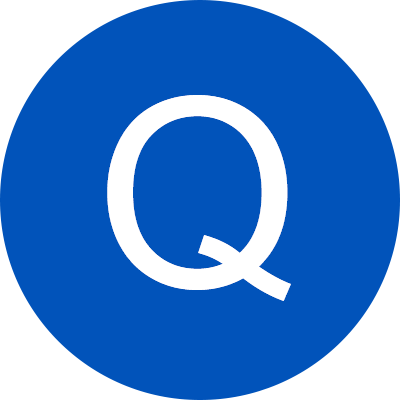
What is the main difference between a ball valve and a gate valve?
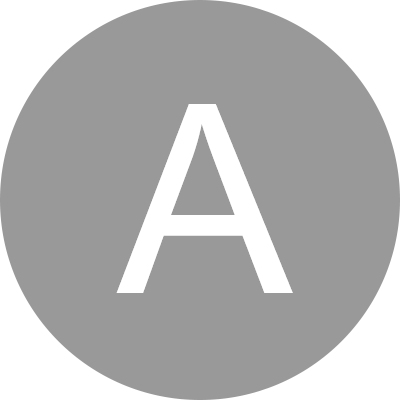
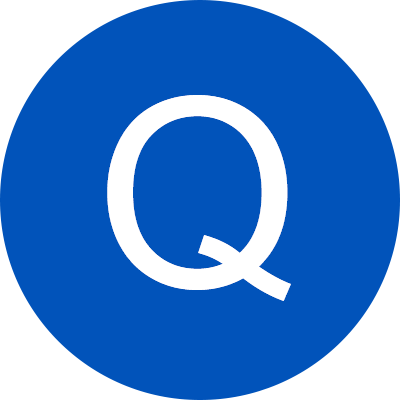
What are API standards? Does the valve need to comply with these standards?
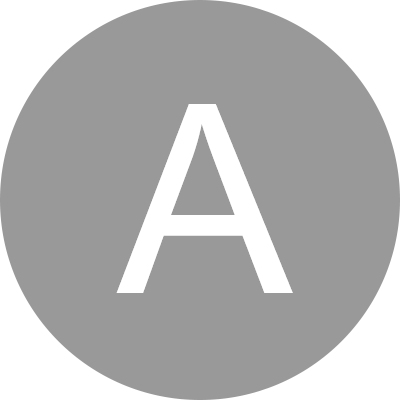
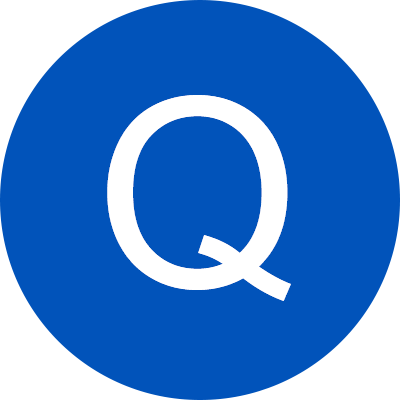
What should I do if the valve is leaking?
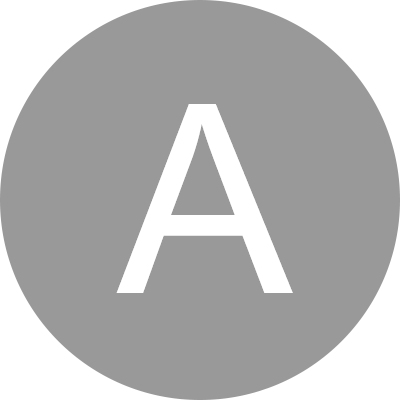
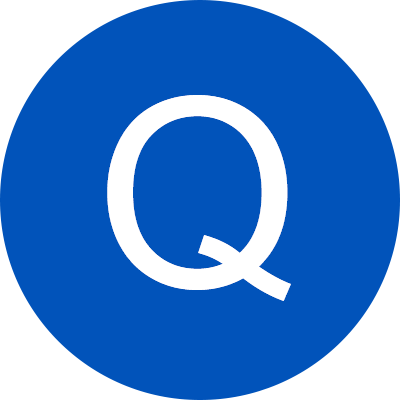
How do I maintain my valves to extend their service life?
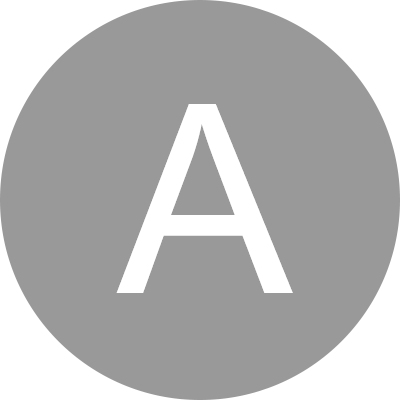
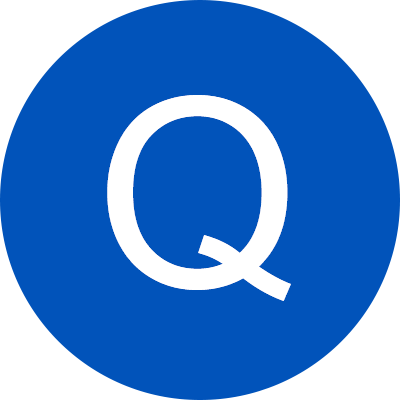
What is the operating pressure and temperature range of the valve?
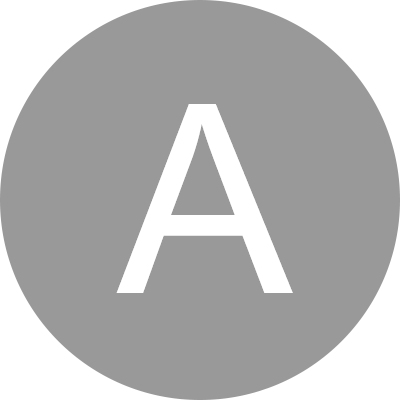
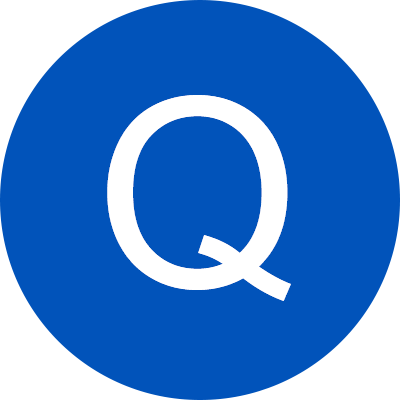
How to determine the size of the valve?
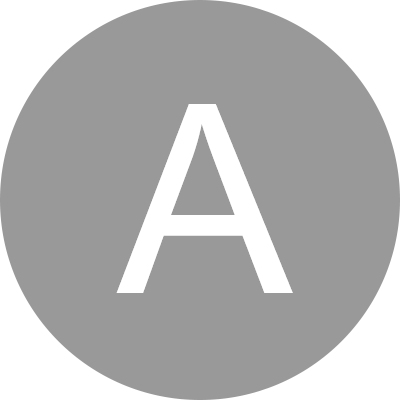
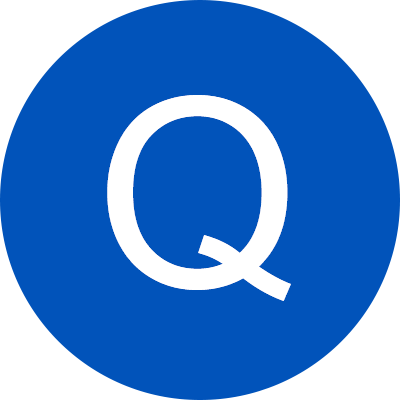
How to choose the right valve material?
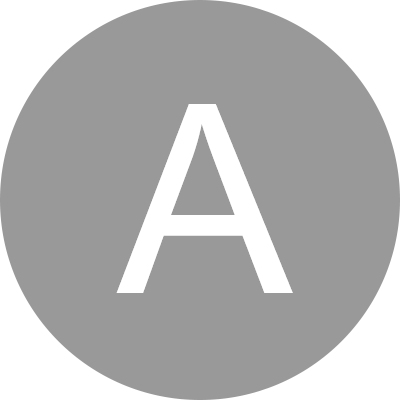
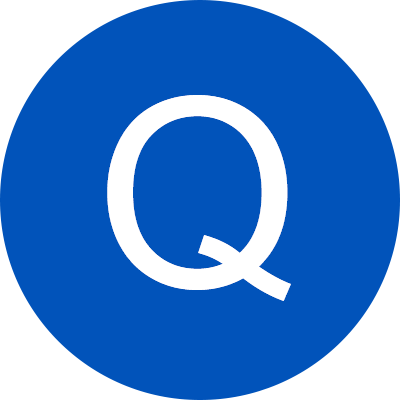
What are the main types of valves?
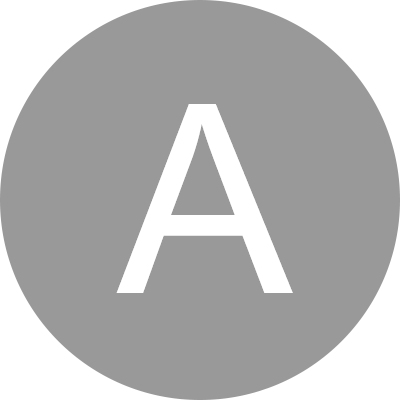
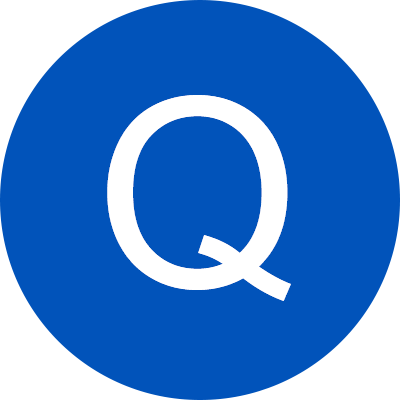
What is a valve?
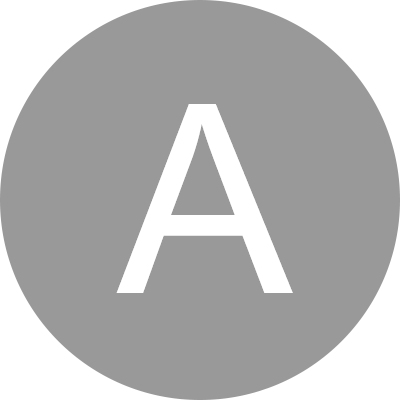

Service Tenet
Service tenet: exchange our "sincerity, enthusiasm and sincerity" for "satisfaction, comfort and reassurance" of users
Service objectives: no complaints about product quality and customer service
Service standard: enthusiastic, considerate, timely and effective

Personalized service

Standardized pre-sales service

Professional real-time process

Diversified training services

Improve after-sales support

Careful follow-up service